
我们新鲜事
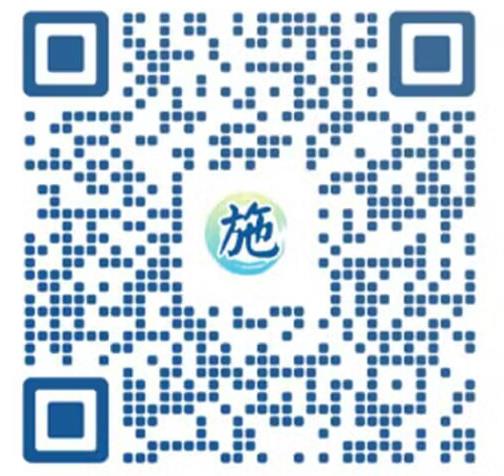
TEL:18925129293
【访谈】施诺斯搅拌脱泡技术如何重塑汽车胶接工艺?
日期:2025-03-10作者:小诺——对话施诺斯科技研发总监李佰明
在上海某超级汽车工厂的电池组装车间里,32台全自动真空搅拌脱泡机正以0.005%的粘度误差控制着结构胶的制备;而两千公里外的长春某新能源汽车基地,施诺斯第五代真空脱泡系统刚刚将某车型的胶接不良率从1.2%降至0.15%。这些数字背后,是广州施诺斯科技股份有限公司在胶水处理领域的持续深耕。我们特别邀请到公司研发总监李佰明,解读这项隐形技术如何支撑现代汽车制造的品质革命。
Q1:汽车制造中胶水应用正经历哪些技术变革?
李佰明:十年前汽车用胶量每台车约15公斤,如今高端电动车已达45公斤以上。从传统玻璃密封到电池包结构粘接,胶水正从"辅助材料"转变为"核心结构件"。这对胶水处理提出三大挑战:一是纳米级填料的均匀分散,二是处理过程中零气泡残留,三是与自动化产线的毫秒级响应配合。这正是施诺斯设备研发的基准线。
Q2:贵司设备如何解决汽车行业特殊需求?
李佰明:以我们为某德系车企定制的SIENOX-MIX Plus混合脱泡系统为例,其搭载的三大核心技术直击行业痛点:
1. 行星式运动结构的公转与自转同步技术:通过“真空负压+动态搅拌”的协同作用,使碳纤维增强胶的分散均匀性提升至99.7%,确保结构胶在碰撞时的能量吸收效率
2. 动态真空脱泡算法:在90秒内将粘度80000cps的环氧胶含气量控制在0.01%以下,比行业标准快40%
3. 智能制造控制系统:与客户MES系统无缝对接,实现每批次胶水的360°质量追溯
Q3:能否分享具体应用案例?
李佰明:在比亚迪某款磷酸铁锂电池项目中,我们的设备解决了超长电芯(1.2米)的封装难题。传统搅拌工艺导致的局部粘度偏差会造成0.03mm的胶层厚度差异,而我们的梯度脱泡系统配合自适应温控,将厚度波动控制在±0.005mm,帮助客户将电池包气密性合格率提升至99.93%。
Q4:如何看待新能源汽车对胶接技术的新要求?
李佰明:800V高压平台和CTC底盘一体化趋势正在改写行业标准。我们正在研发耐高温搅拌模块,有望在180℃环境下连续工作,确保碳化硅导热胶的性能稳定;而针对固态电池开发的全密封搅拌系统,更实现了在氧含量<10ppm环境中的纳米银胶制备,这些技术已在逐步攻克中。
当被问及技术愿景时,李佰明展示了正在测试的AI视觉质检模组:"我们正在将光谱分析技术集成到搅拌系统中,未来设备不仅能处理胶水,还能实时判断胶体化学状态。正如我们的品牌理念——与施诺斯同行,共享工业之美(Partner with Sienox, Experience Industrial Excellence.),我们期待用技术创新重新定义'胶接可靠性'的行业标准。"
从传统车间到智能工厂,施诺斯用十余年时间将搅拌脱泡机的精度提升了两个数量级。在这条看不见的战线上,中国智造正通过一个个0.01%的突破,悄然重塑着全球汽车制造的品质维度。