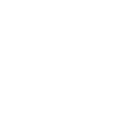
新材料应用
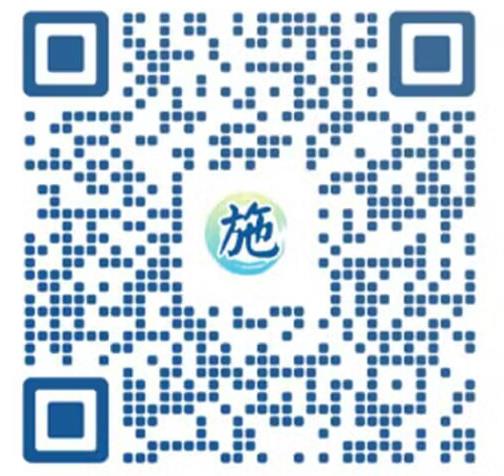
TEL:18925129293
新能源汽车电池封装高精度胶接解决方案,重塑行业新标准
日期:2025-03-10作者:小诺随着新能源汽车市场爆发式增长,电池封装工艺成为决定车辆安全性、续航能力及使用寿命的核心环节。广州施诺斯科技股份有限公司通过自主研发的真空搅拌脱泡技术,以纳米级精度控制胶水处理全流程,为行业提供了从材料到制造的闭环解决方案,助力中国智造领跑全球电池技术赛道。
新能源汽车电池封装的核心挑战
在800V高压平台、CTC(电池底盘一体化)等新技术趋势下,电池封装面临三大技术瓶颈:
结构胶性能极限:胶水需同时满足高强度粘接、耐高温(180℃+)及高效导热需求;
工艺精度缺陷:传统工艺导致的胶层厚度偏差(±0.03mm)引发气密性失效风险;
量产一致性难题:自动化产线要求胶水处理速度、质量与MES系统实现毫秒级协同。
施诺斯新能源电池封装解决方案
1. 纳米级填料分散技术
通过行星式动态搅拌系统(SIENOX-MIX Plus),实现碳纤维、纳米银等增强材料的99.7%均匀分散,确保结构胶在电池碰撞测试中能量吸收效率提升40%,满足UN38.3等国际安全标准。
2. 真空梯度脱泡系统
90秒超快速脱泡:针对80000cps高粘度环氧胶,含气量控制在0.01%以下,杜绝电池包微孔渗漏;
±0.005mm胶层控制:自适应温控模块补偿材料热胀冷缩,助力比亚迪1.2米超长电芯封装气密性合格率达99.93%。
3. 智能制造全链路集成
MES系统无缝对接:实时监控胶水粘度、温度等12项参数,实现每批次数据追溯;
行星式运动结构的公转与自转同步技术:通过“真空负压+动态搅拌”的协同作用,使碳纤维增强胶的分散均匀性提升至99.7%,确保结构胶在碰撞时的能量吸收效率
行业应用案例:重新定义封装可靠性
案例1:磷酸铁锂电池超长电芯封装
针对比亚迪刀片电池项目,施诺斯定制梯度脱泡方案,将胶层厚度波动从±0.03mm降至±0.005mm,电池包能量密度提升7%,且通过IP67防水测试10万次循环验证。
案例2:固态电池全密封制备
在氧含量<10ppm的超洁净环境中完成纳米银胶搅拌,助力客户实现固态电池界面阻抗降低30%,快充寿命突破2000次循环。
未来布局:面向800V高压与CTC技术
施诺斯正加速研发下一代耐高温搅拌模块(180℃连续工作)及碳化硅导热胶处理技术,以应对高压电池热管理挑战。同时,通过AI算法预测胶水固化曲线,实现与焊接、冲压工艺的秒级时序配合,为CTC一体化底盘制造提供底层支持。